Home \ Support
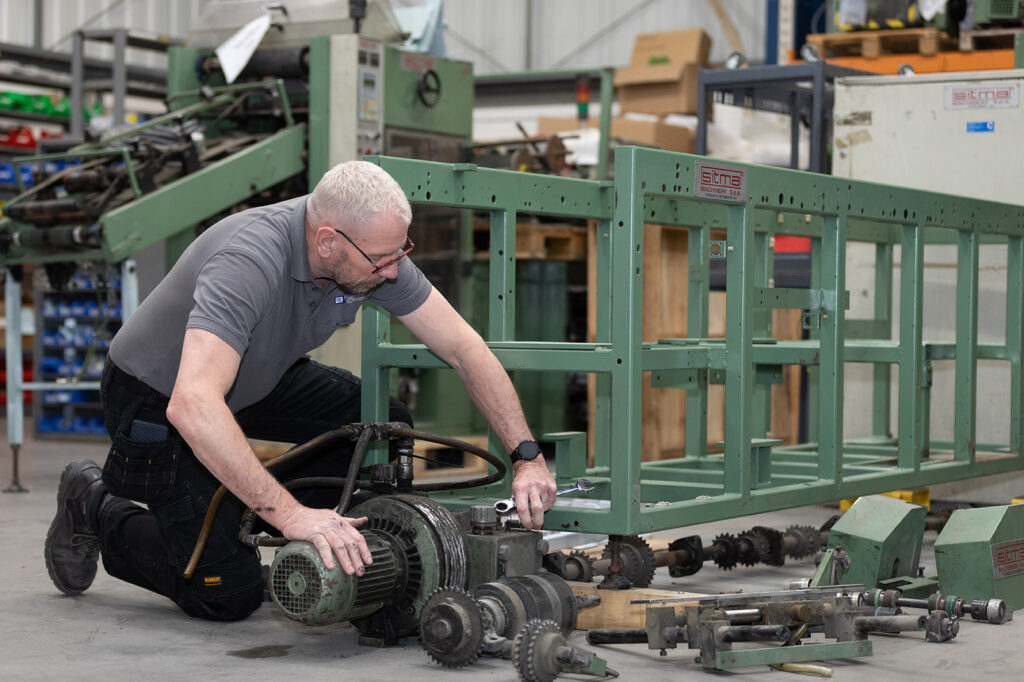
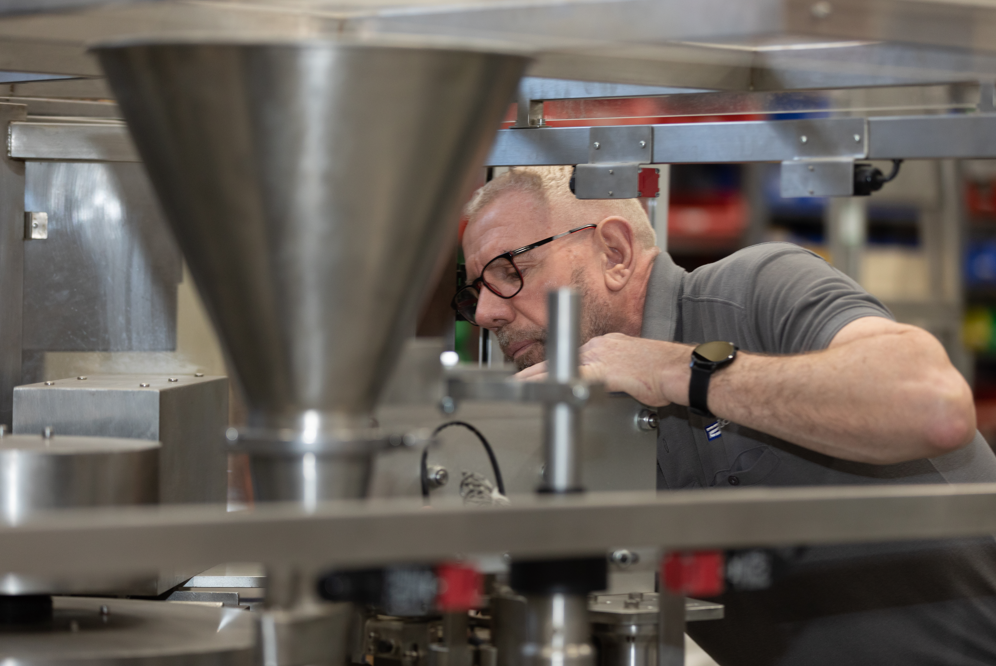
Service
Discover our range of service options and preventative maintenance solutions
We offer a customer-centric approach to installations and provide a range of preventative maintenance, training support and spares packages for the machinery that we supply. In order to maintain machine efficiencies and to help our customers to reduce operating costs we recommend a structured maintenance program.
Routine servicing, that reflects the volume of production from your machinery, will prove economical in the long run, as it will help to reduce breakdowns and downtime. We offer a range of annual service contracts, overhauls, upgrades and emergency breakdown repair.
Do you need service support?
Please contact us and if possible supply the machine type and serial number.
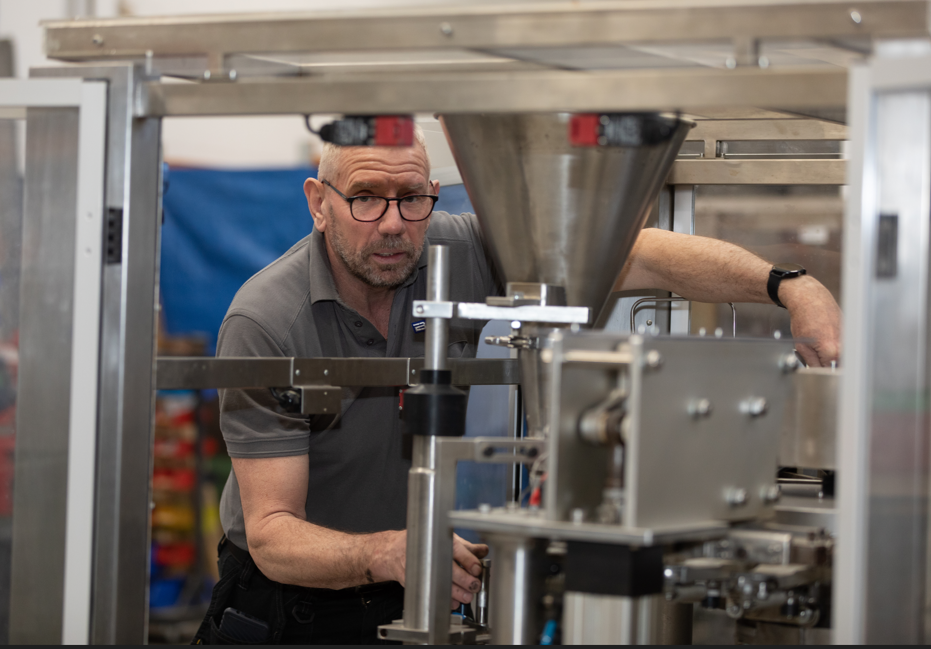
About us
For servicing we use our highly trained, Field Service Engineers.
They have a wealth of knowledge, gained over decades of experience working on a wide range of machinery. We also have access to our manufacturers’ engineers, if there is ever a requirement for specialist knowledge.
Spares
We hold stock of a wide range of regularly needed spare parts. Our experienced team can also help to source anything more unusual from our manufacturers.
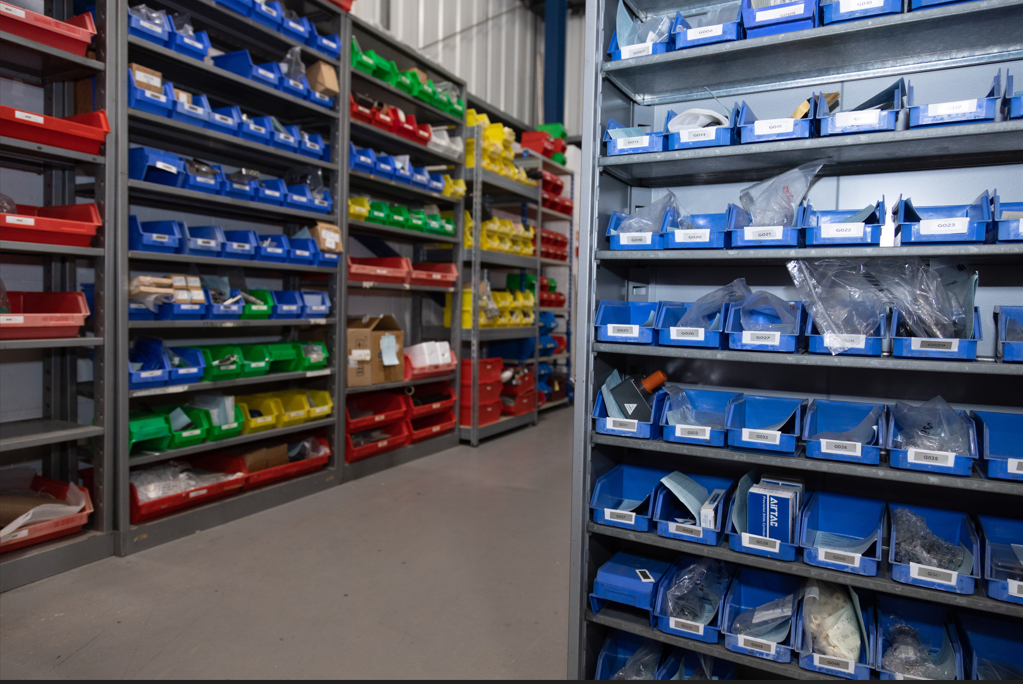
Our preventative maintenance and performance reviews for machinery within the UK and Ireland include:
Full machine inspection:
- Review of running times, hours and product overview
- Module breakdown, listing and group inspections
- Line operation and general overview of usage
- Operator assistance and instruction on routine troubleshooting
- Problem solving and maximising output
Module and part inspection:
- Estimating wear and life expectancy
- Drawing of parts replacement programme (if required)
- Parts and module ‘refurbishment’ with a clean and test
- Output review
Frequently asked questions
Contact us
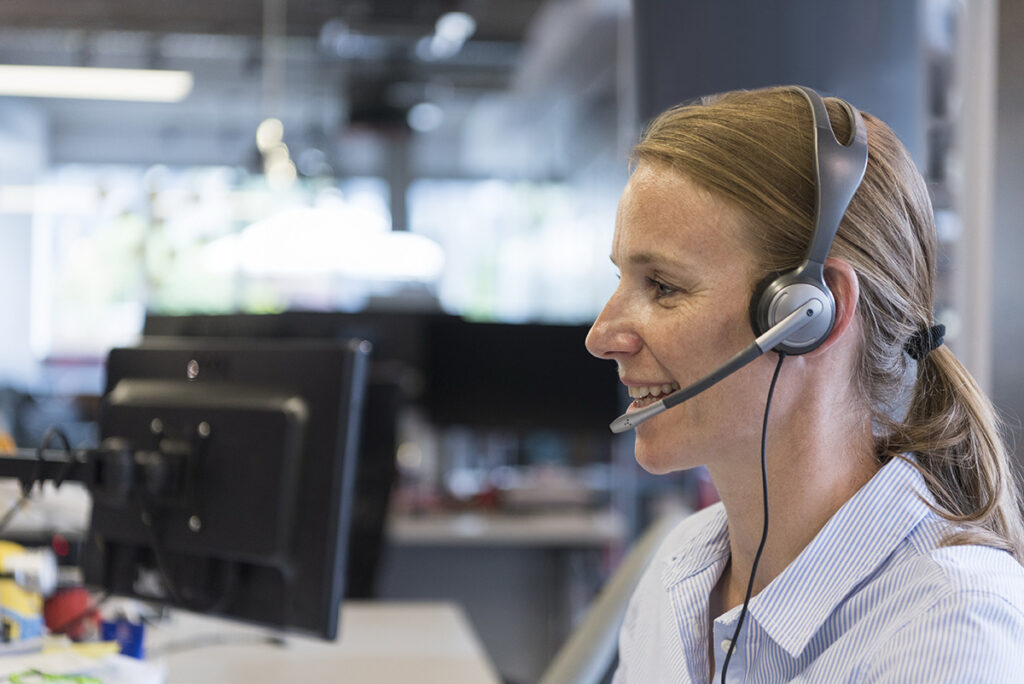